

The modbus server program will need to respond to the HMI requests and somehow store the information required for vendor PLC 2, and it will also need to set a status register to inform the modbus client that there is data for vendor PLC 2.

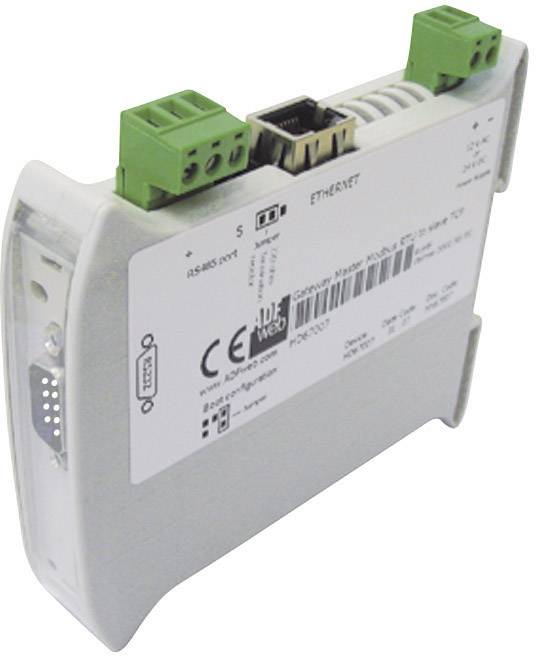
Have a clear and visualized interface to monitor all communicated variables. Modbus TCP, Modbus UDP and Modbus RTU client/server library for. No visualized list for communicated address. Modbus devices communicate using a master-slave (client-server) technique, in which only one device (the master/client) can initiate transactions (called. I'd be keen to gather thoughts on best practices here. Modbus TCP, UDP and Modbus RTU client/server library. In the past the program has handled writes requests from the HMI by forwarding them on to the PLC 2 via the open socket. In addition, Modbus TCP packs its IO data and. The issue I have is that the remote web interface (HMI) must be able to control the behaviour of vendor PLC 2 and Vendor PLC 2 will only allow one TCP connection from the embedded PC. A client must first send a request to a server, then the server answers this request for every transaction. All the data transactions of the Modbus depend on the registered address, function code, and data. The network of communication protocol is formed with one master and 247 slaves with a unique address. Until now, this has worked fine, but we have recently installed a logging client on the network which polls our program very frequently (sub-second) and this has revealed timing issues: the program can potentially take a very long time in its client loop performing calculations and reading PLC values before acting as a server and responding to incoming requests.Įasy solution would be to split the programs into a modbus server and client instance, and keep them both running on the same embedded PC. Modbus Communication Protocol The communication protocol using master/slave or client/server transactions is shown below. So the Server can be configured to send a Report to the Client (s) every time the CB position.
#MODBUS SERVER VS CLIENT PLUS#
Client/Server does everything Master/Slave does as above PLUS the Server can automatically send information to the Clients. Responds to a variety of TCP read and write requests from web interfaces and laptops on site. The Master would have to poll other information to eventually detect that a protection trip occurred followed by the reclosure. It reads from a number of vendor PLCs (servers) on site, performs calculations and sends control commands back to the PLCs based on the data received across the site.
#MODBUS SERVER VS CLIENT DRIVER#
I am working on a legacy modbus program for an industrial SCADA system.Ĭurrently, the c++ program acts as both a modbus TCP server and client. The Modbus TCP Ethernet driver works in conjunction with TOP Server to provide data exchange between OPC UA, OPC DA, SuiteLink and DDE clients and PLCs.
